Reducing Recall Risks with Squid Ink
The True Cost of Recalls in Food Manufacturing
For food manufacturers, a product recall can be devastating—not just financially but also in terms of brand reputation and consumer trust. According to the FDA and USDA, 547 food recalls occurred in 2023, a 20 percent increase from 2020’s total of 454 recalls.
The Grocery Manufacturers Association (GMA) and the Food Marketing Institute (FMI) estimate that the average direct cost of a recall is $10 million, covering expenses like product retrieval, disposal, and regulatory fines. Indirect costs, such as lost sales, lawsuits, and damaged brand reputation, can drive that number even higher.
What Causes Most Recalls?
The leading causes of food recalls between 2020 and 2023 included:
- Undeclared allergens (40 percent) – Missing or incorrect labels leading to allergen exposure
- Bacterial contamination (21.1 percent) – Pathogens like Salmonella, Listeria, and E. coli
- Foreign object contamination (11.6 percent) – Glass, metal, or plastic fragments in products
A significant portion of recalls—56 percent according to a Queen’s University study—stemmed from operational mistakes like:
- Incorrect labeling
- Presence of an undeclared ingredient
- Contamination during the production process
These issues highlight the importance of clear, accurate product coding, traceability, and barcode validation to reduce recall risks.
Product Coding: The First Line of Defense Against Recalls
Accurate, high-quality printing of lot numbers, expiration dates, barcodes, and ingredient statements is essential for product traceability and recall prevention. Manufacturers need the right coding technology to ensure compliance and prevent labeling errors.
Piezo Ink Jet for High-Resolution Secondary Packaging Codes
Example: CoPilot Family of printing systems
For cartons, trays, and cases, hi-res piezo printing provides high-resolution, scannable barcodes and text.
How it helps prevent recalls:
- 360 dpi high-resolution printing ensures sharp, scannable codes for accurate tracking
- Fast-drying, no-mess ink cartridges prevent ink smudging that could make codes unreadable
- Dark print offers more contrast and improved bar code scannability
- Touchscreen control and message storage reduce manual entry errors and mislabeling
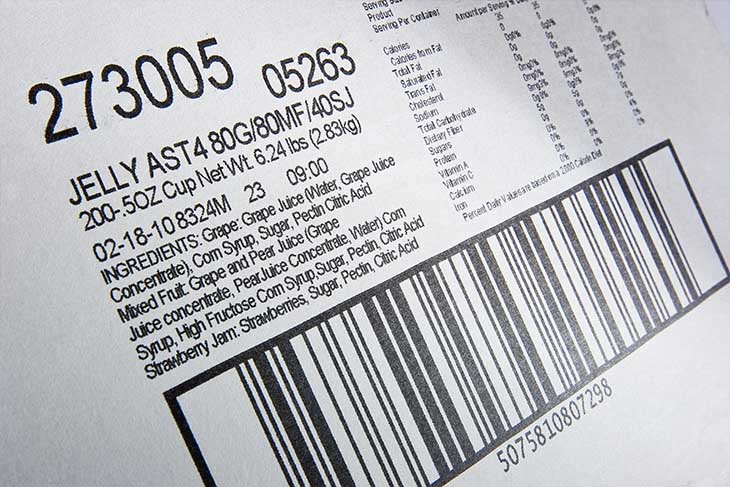
Continuous Inkjet (CIJ) for High-Speed Primary Product Coding
Example: JetStream CIJ
For bottles, pouches, and flexible packaging, continuous inkjet (CIJ) printing provides fast, durable coding on porous and non-porous surfaces.
How it helps prevent recalls:
- Variable data printing allows real-time updates for expiration dates, batch codes, and allergen labeling
- High-speed marking (1,000 ft/min) ensures products are coded accurately without slowing production
- Self-cleaning printhead prevents errors from clogged nozzles, reducing downtime
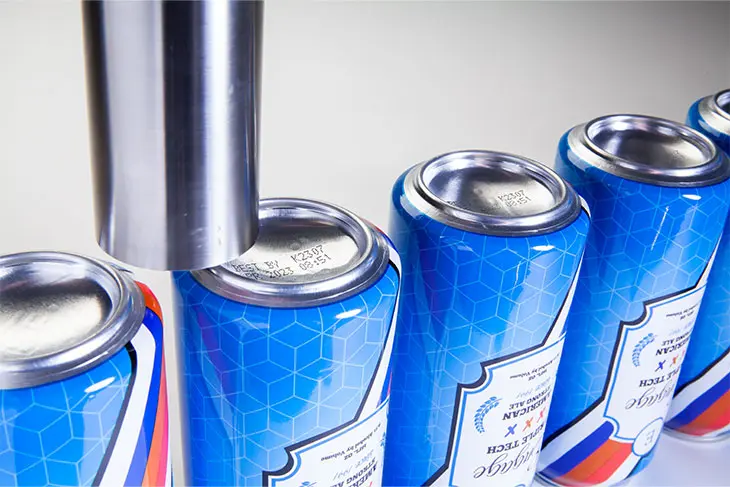
Laser Coding for Permanent Marking
Example: SQ-310 CO₂ Laser
For industries requiring permanent, high-contrast coding, laser marking eliminates the risks associated with ink-based printing.
How it helps prevent recalls:
- No ink, no smudging, no fading—ensures product codes remain readable throughout the supply chain and product lifespan
- Ideal for frozen or high-acidity foods, where ink-based codes may degrade over time
- Anti-counterfeiting features help prevent fraudulent labeling or supply chain fraud
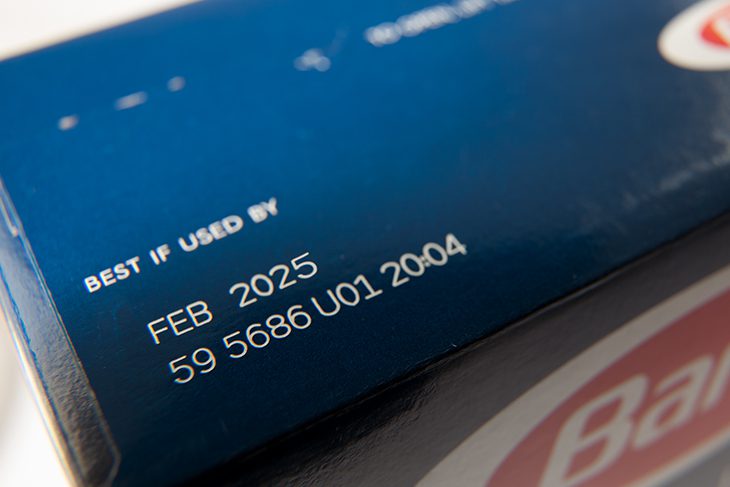
Barcode Validation: Ensuring Every Product is Traceable
Even with high-quality coding, barcode errors can still cause recalls. If a barcode is misprinted, unreadable, or incorrect, entire shipments may be rejected by retailers or require costly recalls.
Why Barcode Validation is Critical
- Ensures barcodes are scannable and correct before products leave the facility
- Prevents mislabeling errors that lead to undeclared allergen recalls
- Meets FDA and USDA compliance standards by verifying traceability data
How SquidCheck Protects Against Barcode Errors
- Uses Cognex readers to scan every barcode in real time and confirm accuracy
- Automatically rejects incorrect or unreadable codes before products leave the production line
- Captures and stores barcode performance data for compliance reports and operational improvements
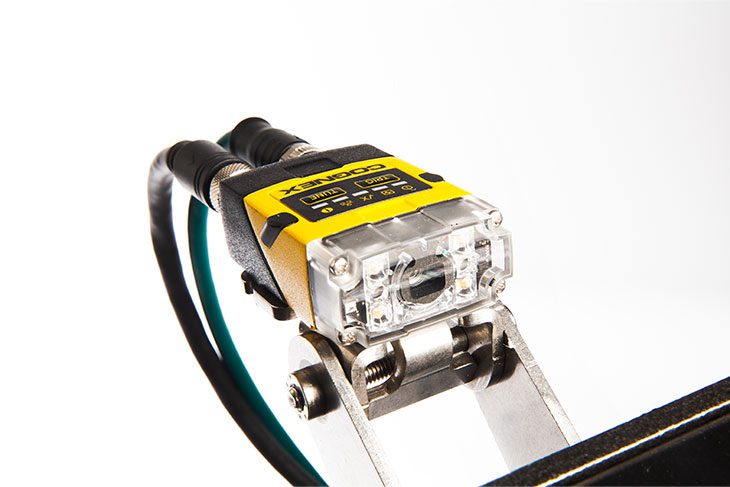
The True Cost of Recalls: Why Traceability Matters
A recall affects more than just a single batch of products—it can have long-lasting consequences.
- Financial losses: The $10 million average recall cost does not include indirect damages like lost customers and legal fees
- Retailer rejections: A single barcode error can result in entire shipments being rejected, leading to lost sales
- Brand reputation damage: Consumers lose trust in a brand after a recall, impacting long-term sales
How Traceability Minimizes Costs
- Ensures fast identification of affected products in case of a recall
- Minimizes the scope of recalls by tracking batches more accurately
- Prevents supply chain fraud by maintaining a clear record of product movement
A Complete Recall Prevention System: Integrating Coding and Validation
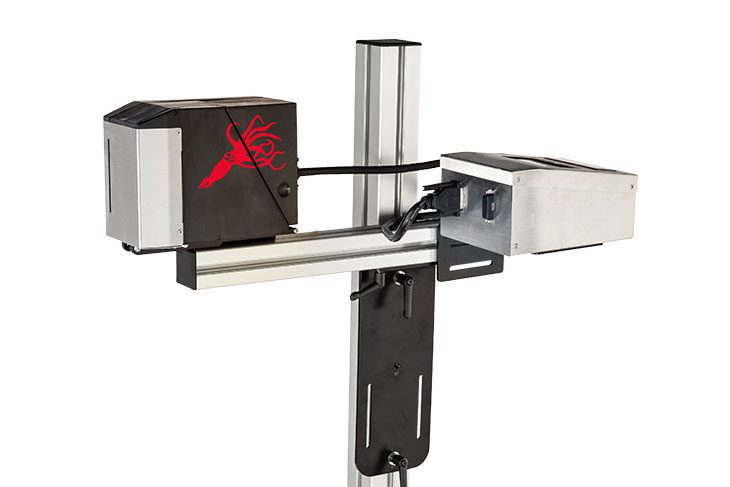
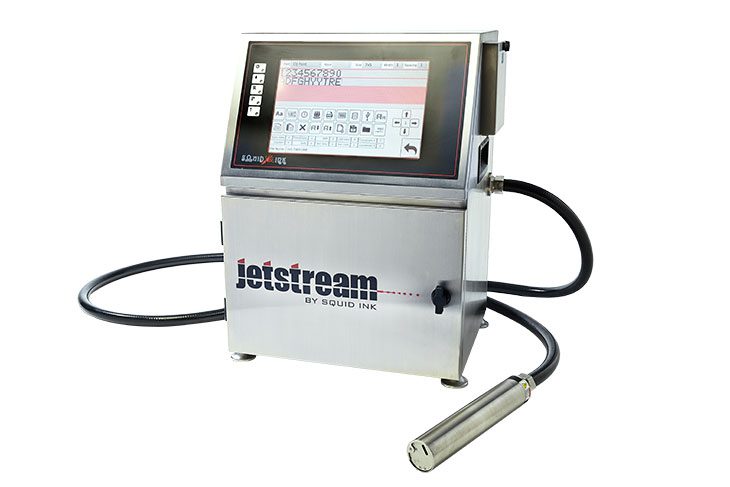
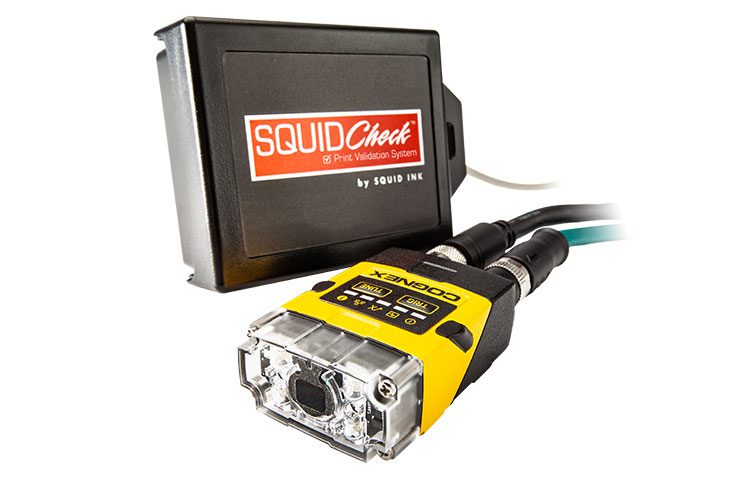
How Manufacturers Can Build a Fail Proof Traceability System
- Use a mix of printing technologies (Piezo, CIJ, Laser) for clear, accurate, and durable coding
- Implement real-time barcode validation (SquidCheck) to catch errors before shipping
- Leverage data from validated scans to continuously improve production efficiency
The Result
- Fewer recalls, fewer fines, and lower financial risks
- Stronger retailer and consumer trust
- A more resilient, compliant, and profitable operation
Final Thoughts: Protect Your Business from Costly Recalls
With 547 food recalls in 2023 and an average recall cost of $10 million, manufacturers cannot afford to take risks with labeling and traceability.
Investing in high-quality coding and barcode validation ensures:
- Accurate product identification
- Faster, safer recalls if necessary
- Compliance with FDA and USDA regulations
Want to improve your traceability system and reduce recall risks? Contact Squid Ink today to learn how CoPilot Piezo, JetStream CIJ, SQ-Laser, and SquidCheck can help protect your products, your brand, and your bottom line.