Bottle Coding: Squid Ink Featured in Wines & Vines
Lower Risk with Winery Lot Traceability Here’s What Works: Setting up a system for quality assurance from bottling to distribution
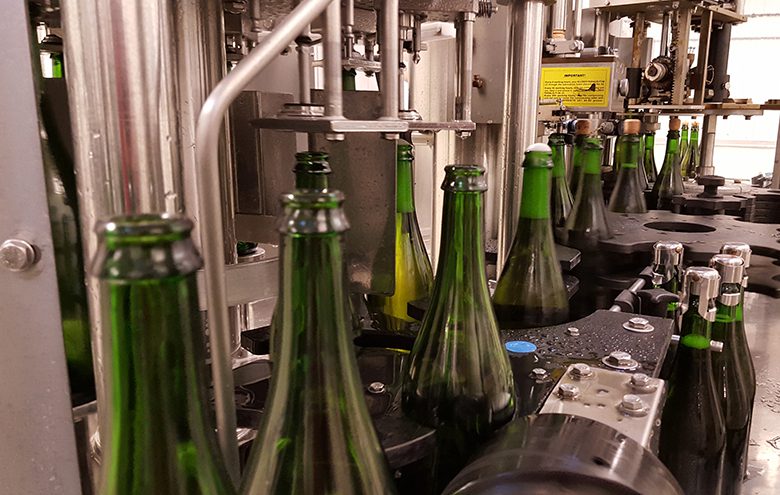
Lot traceability begins on the bottling line where bottle coding is a crucial step to ensure any quality assurance program is effective
San Rafael, Calif.—You bottled 1,000 cases of 2016 Chardonnay over two days. Near the end of the run, your sterile filter plugs, with about 80 cases left to bottle. You grumble about using another expensive filter cartridge. You have an eight-person bottling crew waiting around, so you rush the filter preparation process and skip bubble testing. Three months later, you learn that you’ve had a few customer complaints of cloudy wine that’s also a little fizzy. You’re worried that you have a giant problem and might need to recall the entire vintage from the market and your warehouse. A scenario such as this will test your quality-assurance and lot-traceability systems. For many, lot traceability is considered another “have to” of useless government paperwork or is easily dismissed because wine isn’t cheese. It can’t kill you. Siemens is Europe’s largest industrial manufacturing company, making everything from skyscraper fire-safety systems to medical diagnostic devices to industrial-automation equipment. Its quality standards are among the highest in the world, and if the company makes things incorrectly, it can kill you. On Siemens’ website, lot traceability is defined as the “readily available access to the complete history of all manufactured lots, batches and serialized units, spanning production in multiple plants. It includes materials consumed, processes and equipment utilized, parametric and quality data collected, exceptions, rework, dates and times, and electronic signatures.” Sounds as if they gave this some thought. The 2011 Food Safety Modernization Act has put a new focus on lot traceability, requiring wineries to keep records of all materials that went into the wine. In addition, the FDA has stepped up winery inspections and audits to ensure actual compliance. But even if it wasn’t required by law, there are many good reasons to institute a real lot-traceability program. In interviewing a diverse group for this column — a winemaker at a small premium winery with an outstanding brand; an expert with an enormous wine conglomerate; a leading expert in bottling quality-assurance processes; and a manufacturer of packaging- identification systems — it became clear that improving quality assurance and lot traceability will provide significant value to any winery. The single most common theme in all interviews is that your bottle’s label does not define a “lot” according to Siemens’ definition and that a proper approach reduces the winery’s economic risk exposure in the event of a post-bottling problem. Going back to our hypothetical 1,000 case Chardonnay bottling: Without a good lot-traceability system: Ron Varner, director of bottling and technical services for G3 Enterprises —an integrated “grape to glass” packaging and services supplier in Modesto, Calif. — said, “If you don’t have the ability to isolate the problem within the run, then you have to assume the problem affectted 100% of the 12,000-bottles.” If it turns into a product recall and you have only the “2016 Chardonnay” label as your lot identification, then you have to recall the entire run. At $20 per bottle, the potential loss is $240,000. With a good lot traceability system: You can have the problem bottles returned (or even just get a photo of the inkjet bottle code) and identify exactly when these were filled; what tank and sterile-filter cartridges were used; and the specific lots of glass, closures, capsules and labels by vendor, production date, etc. In addition, you’d have notes from the bottling days. With bottle codes, you’d quickly be able to narrow down the problem to that new sterile filter and read the line operator’s notes that there had been some concerns about the filter. You’d recall only 1,000 bottles, or 8% of the run, while 92% remains on the market with good confidence the problem has been isolated. At $20 per bottle, the potential loss is reduced from $240,000 to $20,000. “You can still ship the balance of the wine,” Varner said of using a robust traceability system. “You can be precise. It’s always better to remove just the tumor instead of an entire limb.” In addition, the financial impact of a quality problem goes beyond the direct loss of product. Kristin Belair, head winemaker for Honig Vineyard & Winery in Rutherford, Calif., reminds us that even “a few bad bottles can do a lot of damage to a brand,” and anyone who has poured a “bad bottle” for a key account or reviewer would agree. Starting the process Installing proper lot traceability seems daunting, as the typical small winery has no dedicated quality- assurance manager or purchasing manager and likely doesn’t use a big JD Edwards enterprise software system. Your week is already jampacked with getting your barrels topped, bottling supplies ordered and making a Costco run to get more toilet paper. (The Costco comment honors the life of my friend, winemaker Dave Stevens, whom we all miss dearly.) Jennifer Murray is vice president of quality for wine and spirits for Constellation Brands. With extensive experience in quality and regulatory issues, Murray recommends starting by forming a cross-functional team to include production, quality assurance, procurement and accounting. In a small winery, that may be just the owner, winemaker, bookkeeper, plus whoever orders packaging supplies, as they are the first control in the process, and the person who handles consumer complaints, as they cover the last control point in the process. (In a small winery, it’s likely that one of these people also does the Costco run when you’re out of town.) This team should meet to develop a process and activity map that identifies and documents your everyday activities. Murray said, “going through the process can be an eye-opener,” as it shines light on gaps in your current methods and record-keeping. After completing the process map, then create a document list so that you can confirm completion of each activity. This document list forms the start of your lot-coding system. Ultimately, all numbered documents will culminate in a unique master number, your lot code, which identifies every piece of documentation for the lot. At Constellation, lot-traceability and coding processes are continually being evaluated and improved. Log the data: Ashley Egelhoff is assistant winemaker for Honig Vineyard & Winery, responsible for its quality-assurance programs. According to Egelhoff, logging the data is straightforward as “existing wine production software is already set up for this.” Honig uses the blend software and cellar-tracking module from Orion Wine. Varner at G3 adds, “You can record with ink and paper at the bottling line, and then transfer later to an Excel spreadsheet or your production software.” Pre-bottling: Much of what you should be doing pre-bottling is ensuring quality and pre- venting problems. In addition, Egelhoff notes that any future insurance claim requires the winery to provide baseline pre-bottling data showing the wine was in good condition at bottling. Honig does these pre-bottling analyses: free and total SO2, pH, TA, VA, dissolved oxygen residual sugar (even if you believe it’s dry), CO2, heat and cold stability for whites, malic acid for reds, and microbiological testing for sterility; plus tests for spoilage byproducts such as 4EP and 4EG for Brettanomyces and TCA for wood corks. During bottling: This is where your planning gets tested. Varner said you should keep it simple and recommended using — and logging the use of — product sequentially, e.g., cork box No. 1, cork box No. 2, etc. on bottling day. Varner stressed the need for good record- keeping for anything that touches the wine, such as bottles, closures and sterile filters. Belair stresses testing filter integrity at the start and end of each day and logging the time and date when you change to a new one. Bottle coding: The group consensus is that lot traceability works only with a bottle code. While case coding should be done as well and is helpful at the warehouse level, the consumer buys and makes a complaint about a single bottle. Without an identifying mark on that bottle, you will likely return to recalling your entire run of 2016 Chardonnay. Chad Carney, vice president of marketing and corporate communications for Squid Ink in Brooklyn Park, Minn., sells inkjet bottle-marking machines starting at $6,800. Laser etching is more expensive and provides a permanent mark, as it etches rather than relying on ink. Squid Ink’s marking device mounts on the bottling line conveyor and prints on bottles as they move by. Carney said data collected should be compatible with whatever software a winery is using, from an Excel database to winery production software to a JD Edwards platform. Squid Ink’s case-marking equipment starts at $1,800, and its products are sold through bottling-equipment distributors, including Epic Labeling and Veritiv in Northern California. Honig uses a Markem laser etcher for bottles and a case printer with time and date as well as any other required information. Bottling marking is becoming standard on mobile wine lines, as well. It helps the winery and provides protection to the operator from insurance claims. Squid Ink supplies glass and case-marking systems to many mobile-bottling companies. As an example, all three of G3’s mobile glass-bottling trucks have integrated bottling marking. Along with a lot number, the bottles should be marked with a dynamic time and date stamp. Varner recommends using Julian dates, a numerical date format that combines the current year and the number of days since the beginning of the year. For example, 10:33 a.m. on Feb. 1, 2018, is represented as 10330322018. “Laser printing adds credibility, which re- ally helps regulatory agencies feel better about what you are doing,” Belair said, adding it shows a winery can properly address safety concerns from consumer or supplier. Belair and Murray both noted that the FDA has inspected their respective facilities, with plans to eventually inspect every winery. Post-bottling: This is the time to log any handwritten notes. Honig has a thorough post-bottling checklist. The winery keeps reference samples of everything bottled and measures free SO2 on a regular basis. Winery staff regularly taste all wines post-bottling, every two to three months for whites, and every six months for reds. Belair said that it is worth the extra time to look at wines post-bottling to assure that standards are being met. The future: Squid Ink’s Carney said lot traceability is consistent with consumers’ desire to know the exact sourcing of their food and beverages. “People want to know what they are putting into their bodies,” he said. In produce fields, some are taking farm-to-fork to the extreme, tying a tag to each unit of organic produce, which is tracked via GPS to the field location where it grew. Belair said that while doing lot traceability may be challenging, and it continues to become more complex, “it enables us to use data to determine cause and effect quickly and efficiently, as well as giving us the ability to determine if a potential issue is isolated to a single bottle or if it is of broader concern.” And as Varner said: “It’s never an issue until you have an issue.” Andy Starr, founder of StarrGreen (starrgreen.com), is an entrepreneur, marketing manager and winemaker who provides strategy, management and business development consulting services. A resident of Napa Val- ley, Calif., he holds a bachelor’s degree in fermentation science from the University of California, Davis, and an MBA from the University of California, Los Angeles.